The construction of a simple gazebo with a shed roof is available to almost anyone who is at least a little familiar with the rules for assembling such structures and knows how to use modern carpentry tools. The process will not take much time if you have a drawing on hand, an estimate has been calculated and all the necessary materials have been purchased.
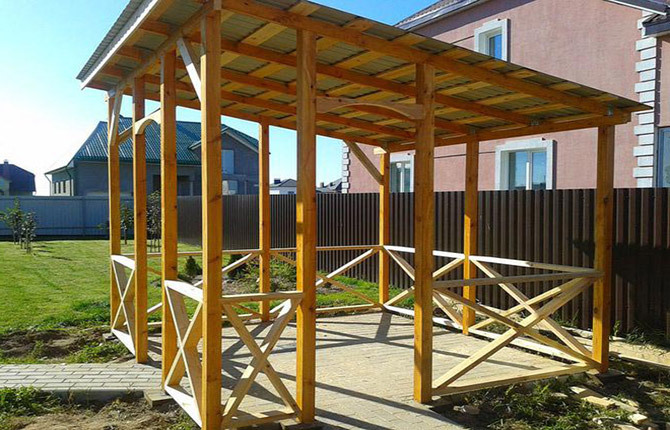
The content of the article:
- Benefits of pitched roofs
- Preparatory stage
-
Arbor schemes
- Features of the shed roof device
-
Do-it-yourself single-sided gazebo from a bar
- Foundation manufacturing
- Bottom trim
- flooring
- Frame assembly
- Installation of supports
- Roof assembly
- Results
Benefits of pitched roofs
The first acquaintance with flat roofs in one slope causes slight bewilderment. The gazebo does not look very presentable, and the simple design is clearly inferior to gable or hip roofs.
But the further use of the gazebo only confirms the correctness of the decision in favor of a pitched roof:
- You can use any roof covering, except for clay and bituminous tiles.
- A simple design of rafters and battens of a shed roof of an arbor.
- If you correctly orient the gazebo on the ground, then the slope can be hidden from the sun's rays. If you expand the building by 180O, then, on the contrary, make the roof very hot.
- Savings on the arrangement of gutters.
The main advantage is that a shed roof very rarely leaks in the rain. In this, the gazebo has always differed from buildings with gable, hipped and hip roofs.
Another plus that few people pay attention to when choosing a roof structure. Single-slope models almost never have condensation on the details of the under-roof space. Even steel supports and struts never rust due to good ventilation. In gable structures, condensation and moisture control have always required regular painting of rafters and racks.
Healthy: Arbors with their own hands made of wood.
Preparatory stage
Construction begins with the choice of a site on the site, the design or scheme of the future gazebo. You will also need to choose the material for the main frame, roof and roofing.
The easiest way is to build a gazebo with your own hands from lumber: boards, timber, lining. For vertical racks, a bar of 150x150 mm is required, for strapping - 50x50 mm. All other parts of the frame will be made of edged boards, lining, slats. All wood parts must be planed in advance, treated with bioprotection, dried under a canopy in the shade to avoid cracks.
If the building is needed for temporary rest during work, for example, when building a house, then a gazebo can be built with your own hands from scraps of lumber, slate and sheet metal. Shed gazebos for long evening gatherings with a barbecue are built according to a capital scheme with a foundation and an additional podium (platform).
It would be right to draw up a step-by-step instruction for assembling a gazebo for yourself. This will make it possible to draw up an estimate in advance and calculate the number of metal fasteners with a corner, "butterflies", threaded studs, washers-gaskets before the construction of the frame begins. In addition, you will need oil varnish, paint, roofing.
Of the tools you will need:
- table circular saw;
- grinder with circles;
- belt grinder;
- building level;
- carpentry set: saw, hammer, nails, squares, tape measure.
In addition, you will need a table or a carpentry workbench, on which it will be possible to cut blanks for the gazebo frame. In the process of assembling the frame of the gazebo, you will have to grind and cut a lot of wood. On the "knee" sawing and planing is absolutely impossible. Otherwise, the amount of marriage will double, and the frame itself may turn out to be not quite even.
You will also need a shovel, cinder block, cement, sand, crushed stone, pieces of glass roofing material.
Arbor schemes
Next, you need to choose the design of the frame and roof. According to the device, gazebos are open or closed. The structures of the first type include those in which the front or one of the side walls is completely open, without any supports, cladding or fencing.
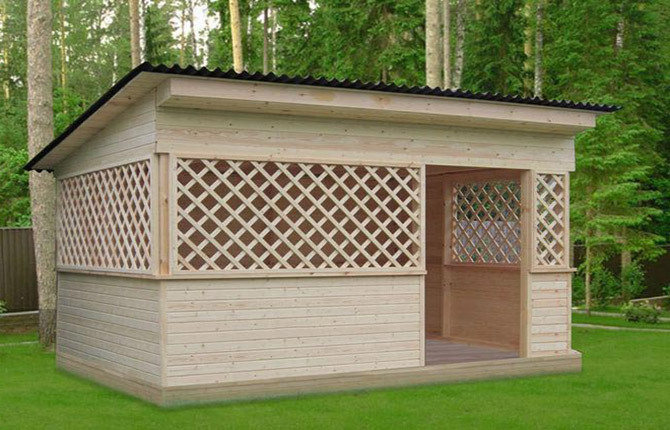
Closed always with a fence, sometimes quite dense wall cladding. Such structures are sometimes called winter.
If you plan to build a summer version of a universal gazebo, then an open design is best. It is more convenient to use, does not require regular maintenance of fences. Such gazebos are very fond of the owners of cottages. It can be used as a shed to store everything from a car to building materials, firewood and new crops.
Closed models provide more comfort in spring and late autumn. For example, in rainy and windy weather it is better to sit out in a closed gazebo.
Useful: How to make a gazebo from a profile pipe with your own hands.
Features of the shed roof device
Traditionally, to form a roof slope, the front supports were made higher than for the rear pair.
Since a shed roof with a crate always created horizontal pressure on the front supports, both racks were connected by a transverse beam and several struts to increase the rigidity of the structure. This made it possible to use thinner and lighter battens or boards for battens and counter battens.
Thus, the angle of inclination of a shed roof could be made quite large, up to 30O. This is important if the gazebo is planned to be built in an area with a lot of snow in winter.
With the advent of fully open (Italian) arbors, they began to make a shed base for the crate from a heavier, massive beam. The angle of inclination of a shed roof has decreased to 5-10O, but the shadow area has increased.
No need for a horizontal crossbar. The rigidity of the gazebo frame is ensured by deep installation of massive supports into the ground and a thickened beam used on the ceiling.
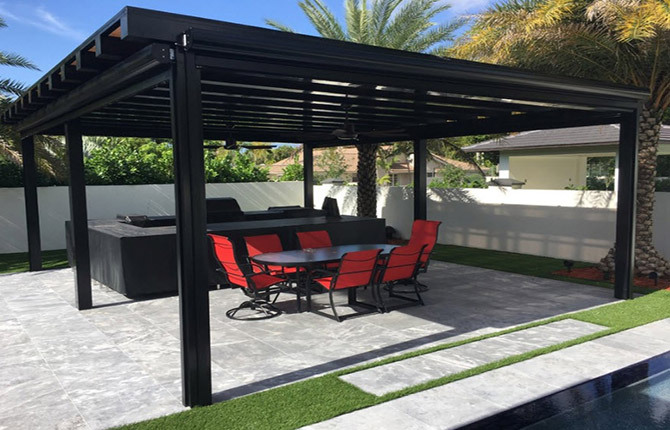
This type of pitched roof is only recommended for hot areas where it rains rather than snows in winter.
Do-it-yourself single-sided gazebo from a bar
For construction, a classic closed-type project with a podium, a fence, a shed roof and a roof made of painted profiled sheet metal was chosen.
The planned size of the building is 3x4 m. One of the side walls and the back of the gazebo is sewn up with OSB. As a result, the structure is sufficiently rigid and durable to stand without repair for 10-15 years.
Foundation manufacturing
The gazebo will be installed on poles made of cinder block. This is the cheapest and most reliable option for bulky wooden buildings. The site must be contoured (marked dimensions) and the entire fertile layer, plant roots and soil must be dug to a depth of 10 cm. All this must be removed from the site.
Further, at the corners of the rectangular contour, as well as in the middle of the sides and in the center, pits of square section 60x60 cm 15 cm deep are dug. Gravel and sand are poured at the bottom of the pits, a pillow is shed with a liquid sand-cement mixture.
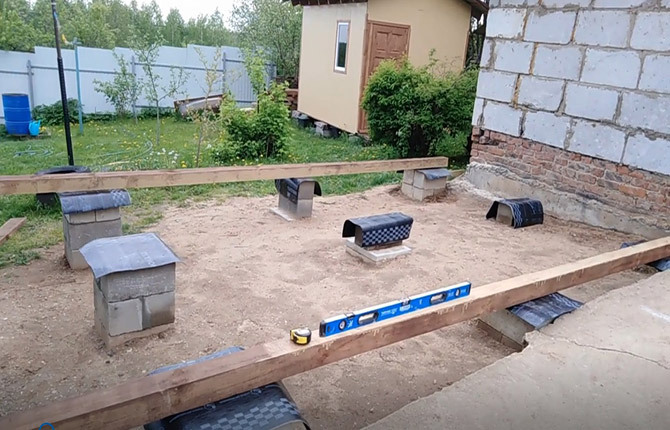
On a base that has not yet hardened, a cinder block is laid out in pairs. The total height of the column above the ground should be 35-37 cm. Until the solution has set, you need to adjust the height of the pillars. To do this, several masking cords are pulled between the extreme supports, the highest ones are upset with gentle blows with a hammer. As a result, the heads of all columns should be located in the same plane.
After leveling, the site is covered with a mixture of sand and gravel screenings, and pieces of glass roofing material are glued onto the supports with molten resin.
Bottom trim
The next step is to bind the lower tier of the gazebo to the columnar supports. For the lower strapping, a bar with a section of 100x100 mm is used. Since it bears the entire load, you can take a more massive material, for example, if a brick barbecue stove is to be installed in the gazebo.

Initially, for each side, you need to mark the beams along the length, and then cut the ends for the corner joint into a “half-joint”. Next, you will need to decompose the blanks into poles around the perimeter, so far without joining at the corners. With the help of a small amount of masonry mortar, it is necessary to align the position of each beam with the horizon, and then fix each beam by placing oppression weighing 15-20 kg on top of it.
Now you need to fix the details of the lower trim on the surface of the posts. Using a carpenter's brace or a drill with a 15 mm drill, we drill holes through the tree until the tool rests on the cinder block.
Next, you need a powerful electric drill with a 12 mm drill. A hole is drilled in the cinder block to a depth of 15 cm. On the surface of the beam, a hole of 25 mm to a depth of 15 mm is needed. This is necessary to hide the nut in the body of the timber.
To fix the timber strapping, galvanized steel studs M12, 20 cm long, are used. We apply masonry glue to the fasteners and carefully screw them into the drilled hole to the full length.
After all the studs have been wrapped, it is necessary to wait 6-7 hours for the glue to harden. Only then can the washers be carefully laid and the nuts tightened.
Before tightening the nuts into the hole with the studs, pour 5-7 ml (a couple of tablespoons) of drying oil into the hole. After two or three days, after drying, it will stop the thread and cover the tree, thereby the connection will be protected from moisture.
It is recommended to open the entire harness with a protective varnish, oil paint or just drying oil. In the corners of the strapping, the beam can be additionally knocked down with nails, after dipping them in drying oil or varnish.
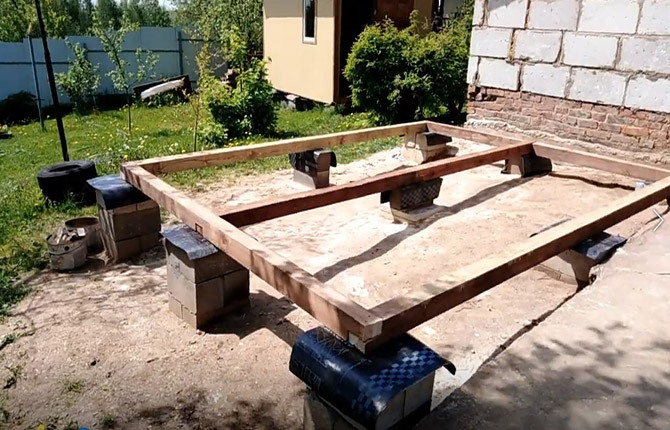
For processing nails and pouring under studs, it is best to use the cheapest varieties of drying oil or cook it for a gazebo with your own hands. This will require approximately 1-1.5 liters of old sunflower oil (can be rancid).
Boil for 7-8 hours over low heat. A dark viscous liquid will be obtained. She processes all the joints and fasteners in the gazebo. Homemade drying oil eventually acquires the consistency of semi-dry glue. Ideal for protecting against moisture parts of a shed roof and the foundation of the gazebo.
Interesting: How to build a comfortable metal gazebo with your own hands.
flooring
Before putting the frame, it is necessary to lay the boards of the future floor. Since logs are not used in the design of the gazebo, a fifty-edge edged board, 150 mm wide, is taken for flooring.
The board is laid on the floor of the gazebo with a small gap (0.5-1.0 mm), this is necessary in order to compensate for the expansion of the tree when the humidity changes.
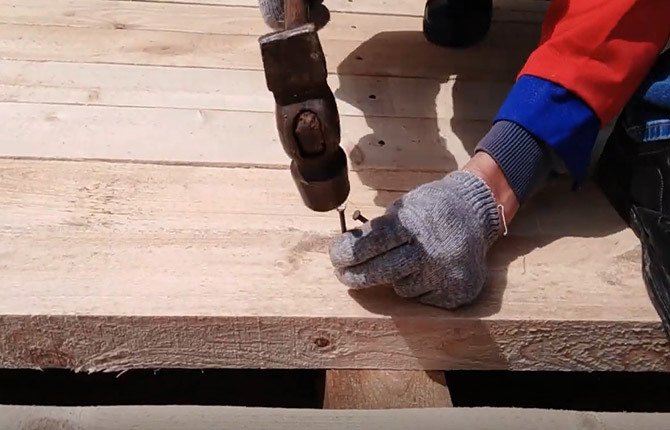
Nails are hammered into the boards in a carpentry way: at different angles, be sure to dip the fasteners in home-made drying oil. Even if the floor in the gazebo is not painted, the nails will still not rust, the floorboards will not rise, there will be no creaking.
Frame assembly
After the floor is assembled and primed at least once with polyurethane or acrylic varnish, you can proceed to the installation of vertical racks and top trim.

First you need to mark and cut out seven permanent vertical supports and one temporary:
- three for the back of the gazebo;
- four, given the entrance and the window, for the facade of the building;
- one temporary will be used to assemble the shed roof frame.
Three pieces are cut out of a bar 100x100 mm, 220 cm long, four facade racks - 250-270 cm each. The temporary support is made of two 20 mm boards knocked down in a package, 220 cm long.
In addition, you will need to cut three horizontal crossbars of 290 cm, 180 cm and 150 cm from the fifty-fifty board. They will be used to equip the gazebo fencing.
Installation of supports
The reliability of a shed roof directly depends on the accuracy of the installation of vertical supports. This scheme does not have paired rafters, due to which it is possible to level and balance the surface. Any error in height will make a shed roof either “humpbacked” or with a hole in the center of the slope.
The first to install the supports from the back side - the extreme left and right, each separately. First, you need to nail a couple of planks or pieces of slab 120-150 cm to the lower harness. After installing the vertical support at the corner, grab it to the flooring with a pair of nails and, after aligning it vertically, fix it with strut strips.
After installation (with struts) of all vertical supports, a beam of the upper trim of the back side is laid. Immediately after laying, another beam is installed on top, but already for the rafters of a pitched roof.
In a similar way, the supports for the front side are assembled, including the laying of the support beam for the pitched roof.
Now you need to align the rear side racks with the front ones. It's like trying to make two sheets of plywood placed vertically parallel. The task is not easy: fitting the frame alone, as well as installing a shed roof, will take a lot of time. At least one, and preferably two, assistants are required.
First you need to cut between the rear corner and front corner along one horizontal cross member. Each bar is immediately nailed to the back (with one nail), on the front pillar, the end is simply inserted into the groove cut in the vertical front pillar. Next, with the help of a tape measure and a building level, it is necessary to adjust the position of the racks, and then hammer the second nail into the crossbar, but already on the front rack of the gazebo.
After alignment, the length of both crossbars must match to within a millimeter, otherwise the pitched roof will turn out to be sloping to the higher side of the gazebo.
If the size of the gazebo is larger than 3x4 m, or if the shed roof is made in two tiers, in addition to the side crossbars, it will be necessary to sew on the "beams" of the ceiling.
After assembling the frame, all joints, angular and linear, must be reinforced with metal plates and corners. This must be done throughout the design of the gazebo and always before the installation of the rafters of the pitched roof. It is clear that the whole tree needs to be varnished.
For the first treatment, a varnish is used, diluted with a double portion of the solvent to the state of "water". It will penetrate deep into the pores of the wood and make the frame of the gazebo insensitive to air humidity. The second treatment is carried out with varnish of the usual consistency, but after the installation of a pitched roof.
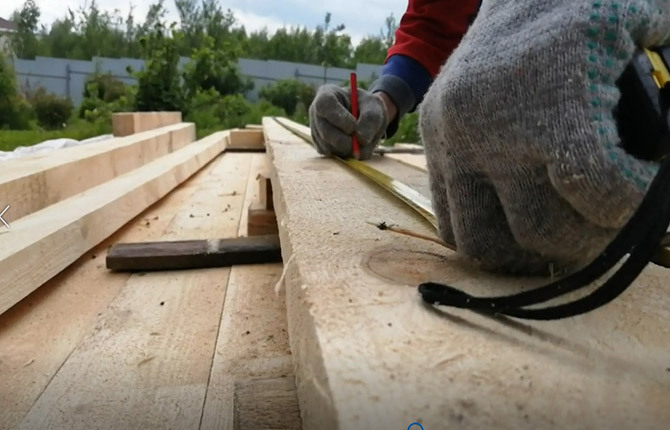
Roof assembly
Now the main thing is to correctly cut the rafters under the pitched roof. Since the roof frame is made according to the classical scheme, you just need to select eight blanks from a 30-40 mm board, it can be thicker, 4 m long.
At first glance, for a shed roof, you can choose a thinner workpiece, for example, an inch. But in this case, you will have to put up props and immediately hem the ceiling with crossbars. So thick rafters for a shed roof are a more profitable solution.

The transverse size of a shed roof will be 0.5 m larger from the facade and rear of the gazebo. This stock is necessary for the arrangement of roof overhangs.
Next, you need to select a couple of boards, the most even and straight. These will be the extreme side rafters of the shed roof - the left and right extreme. We raise both blanks up and set them in their places, while without cuts.
It is quite difficult to visually determine how even the rafters are. This is important, if you do not control it, then the overhang of a shed roof will turn out to be oblique. Therefore, we stretch the paint cord between the ends of the rafters (from the front side), adjust the position of the boards so that it becomes parallel to the beam of the upper harness.
Immediately mark the places on the rafters washed down the grooves. We cut and fasten the blanks, re-stretch the paint cord between the ends. Now we raise all the rafters in turn to the roof, mark the places of cuts along the cord, cut them out and put them in place. The result is a smooth truss frame of a pitched roof.
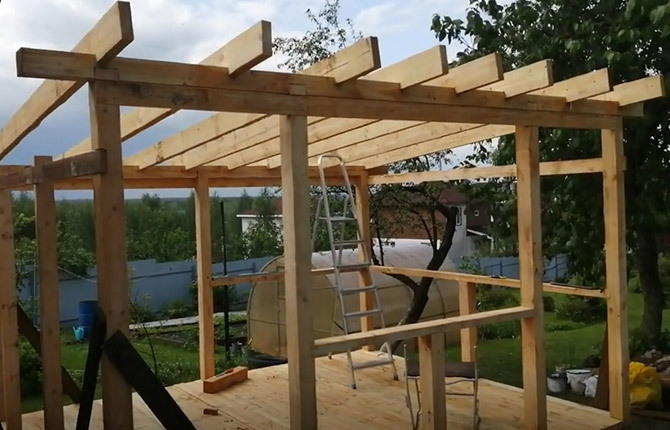
The next step is to sew the battens onto the rafters. You can even use unedged lumber with a thickness of 20-25 mm, a width of 150 mm. The length of the crate for this type of shed roof should be up to 4.5 m. That is, overhangs of 25 cm are obtained on the sides. That's enough for a conversation.
After laying the battens, geotextiles or roofing material are laid. This is necessary to protect the sheathing and rafters of a pitched roof from condensation. On top of the protection, slats 40x40 mm are sewn and the roof is laid. For example, a metal tile or a professional flooring.

If there is a brazier or a stove in the gazebo, then for a shed roof this is the best option. Ondulin in the conditions of the gazebo is enough for 10-15 years; for bituminous tiles, the base of the shed roof will need to be additionally sewn up with continuous sheets of waterproof plywood.
Results
A gazebo with a shed roof can be considered the simplest option available for construction by almost all summer residents and lovers of countryside recreation. All that is required of the worker is to carefully follow the procedure and not save on material.
Tell us about your experience building gazebos. How can a single-pitched roof compete with a double-pitched one? Write a comment, repost the article through social networks and bookmark it, this will help the development of our site!