Es imposible comprar una máquina de soldar y usarla todos los días sin configuraciones adicionales. Este dispositivo requiere una lista de trabajos preparatorios antes de su uso. De lo contrario, no funcionará normalmente. Cómo configurar correctamente una máquina de soldar y qué matices se deben tener en cuenta al trabajar con ella; debe aprender sobre todo esto con anticipación.

El contenido del artículo:
-
Recomendaciones de configuración
- Selección de mezcla de gases.
- Ajuste de voltaje
- Configuración de la velocidad de alimentación del alambre
- Establecer la polaridad correcta
- Configuración de la extensión del cable
- Los fallos más comunes y sus síntomas.
Recomendaciones de configuración
Existen varias características de funcionamiento de la instalación. Cada uno de ellos incide en el correcto funcionamiento del mismo. Debe seleccionar la mezcla de gases, ajustar el voltaje y la velocidad a la que se alimenta el cable. Realice el ajuste de polaridad y el ajuste de la extensión del cable.
Es razonable considerar cada etapa de la instalación de la unidad con más detalle por separado.
Selección de mezcla de gases.
La consideración de cómo configurar correctamente una máquina de soldar debe comenzar con el estudio de las reglas básicas que se deben seguir al seleccionar una mezcla de gases.
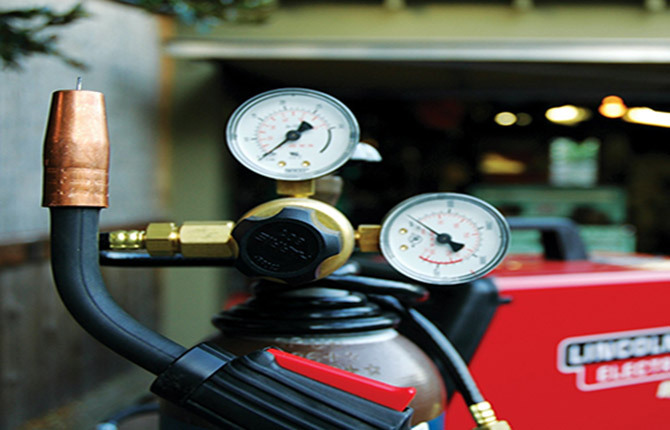
Para no comprometer la integridad de las piezas a soldar y de la propia máquina de soldar, es necesario protegerlas. Para ello, se utiliza gas puro o una mezcla de varios gases en diferentes proporciones; se bombean a la zona de soldadura solo durante el trabajo.
En el caso de utilizar máquinas de soldar semiautomáticas se utilizan 2 gases:
- carbónico;
- argón.
Los gases se pueden utilizar tanto en forma pura como con la adición de varias combinaciones. Para trabajar con diferentes aleaciones y la costura resultante sea de buena calidad, es necesario elegir las proporciones correctas:
- Dióxido de carbono puro (dióxido de carbono).Se utilizan para conectar láminas gruesas y componentes individuales de instalaciones de una pieza en diferentes direcciones. Los materiales con los que se realiza el trabajo están elaborados a base de hierro - hierro fundido y acero. En este caso, con la ayuda de este gas, la máquina de soldar podrá formar correctamente una penetración profunda. El lado negativo del proceso es la formación de muchas chispas. La costura resultante es desigual y estéticamente desagradable.
- Mezcla de gases número 1. La mezcla de trabajo contiene un 25% de dióxido de carbono y un 75% de argón. Debe utilizarse correctamente en los casos en que sea necesario interactuar con láminas metálicas delgadas. Ajustar la mezcla en estas proporciones le permite lograr una costura uniforme.
- Mezcla de gases número 2. Contiene 98% de argón y sólo 2% de dióxido de carbono. Este ajuste de la mezcla de gases es correcto cuando se conectan chapas de acero inoxidable o acero galvanizado. El ajuste también es adecuado para trabajar con aleaciones a base de cobre. El resultado de la conexión de salida es de alta calidad.
Si elige la mezcla de trabajo adecuada, las piezas se conectarán de forma fiable y no se abrirán ni siquiera bajo cargas elevadas debido a su uso intensivo.
Ajuste de voltaje
Siempre se requiere una profundidad de penetración diferente. También difieren el espesor de las láminas y el tamaño de las piezas a unir. Por lo tanto, es necesario ajustar correctamente el voltaje en la máquina de soldar.
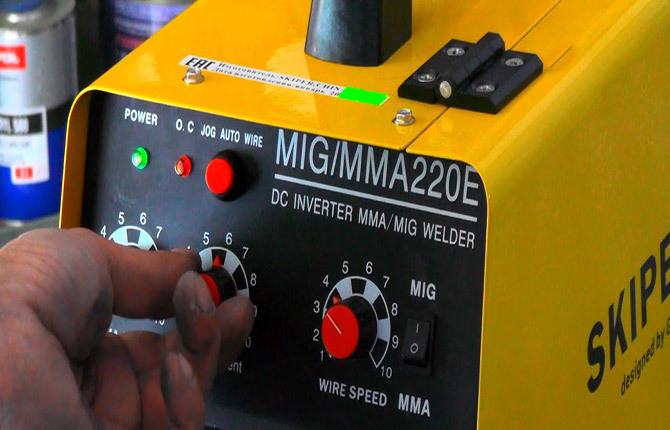
Solo hay una regla: a medida que aumenta la cantidad de energía gastada en fundir la soldadura y la aleación, así como en quemar el arco, también aumenta la necesidad de más voltaje. Al fin y al cabo, es el voltaje el que se encarga de convertir la corriente eléctrica en energía térmica.
El voltaje se ajusta en pasos. En las máquinas de soldar modernas, es correcto ajustar este parámetro en 2 etapas:
- Primera etapa de configuración – en la parte trasera del dispositivo semiautomático se inicia uno de los modos de funcionamiento de la instalación (1º o 2º).
- Segunda etapa de instalación. – selección del nivel de tensión para un modo de funcionamiento específico. Cada máquina de soldar semiautomática siempre tiene un interruptor separado para trabajar con este parámetro.
El voltaje en la máquina de soldar siempre se selecciona entre dos modos: mínimo y máximo. Para facilitar el ajuste correcto del suministro de voltaje, los fabricantes colocan un recordatorio en las unidades que permite ajustar este parámetro a la velocidad de alimentación del alambre. Cada máquina de soldar tiene su propia tabla de modos de funcionamiento.
La tensión de alimentación debe configurarse correctamente. La conclusión es que si lo configura demasiado débil, la profundidad de penetración no será suficiente. La costura formada será excesivamente frágil. Por el contrario, si realiza una instalación con una tensión excesiva, el material de trabajo puede quemarse y quedar inutilizable.
Configuración de la velocidad de alimentación del alambre
La velocidad a la que se alimentará el alambre en la máquina de soldar debe ajustarse solo después de que el voltaje se haya configurado correctamente. La velocidad de avance determina qué tan rápido se derretirá el material. Al mismo tiempo, el funcionamiento también se ve afectado por la tensión suministrada por la máquina de soldar.
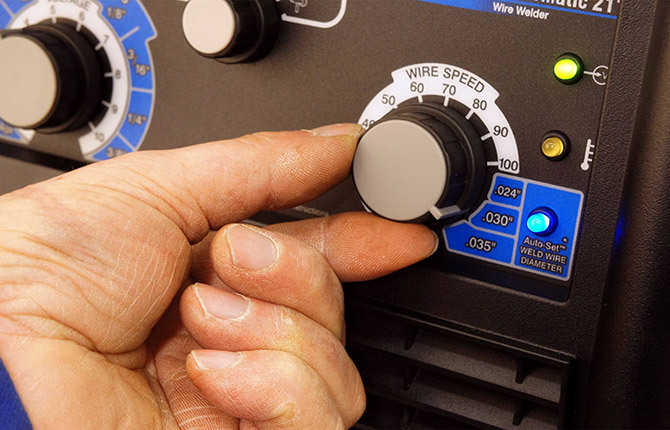
Cuando comienza el proceso de fusión del hilo de soldar, la velocidad a la que comienza a moverse disminuye gradualmente. Es importante configurar correctamente porque:
- Si la configuración del suministro del electrodo no se realizó correctamente, cuando entre en contacto con estructuras metálicas, su forma comenzará a cambiar antes de que comience el proceso de fusión. El electrodo de la máquina de soldar comenzará a adherirse a la superficie de trabajo, lo que provocará la formación de flacideces innecesarias. La costura quedará intermitente y descuidada.
- Si la alimentación del filamento se ajusta de manera que avance demasiado lentamente, el electrodo corre el riesgo de quemarse antes de que tenga tiempo de derretirse. Al mismo tiempo, la punta del soplete de la máquina de soldar se obstruye. La costura resultante será ondulada.
En una máquina de soldar, es necesario ajustar la alimentación de alambre con mayor frecuencia, porque después de cada cambio de voltaje o uso de otros hilos de relleno, la configuración de alimentación de alambre se pierde. Muchos modelos de unidades le permiten seleccionar correctamente la configuración de suministro de electrodos en modo automático (todas las acciones se realizan electrónicamente).
Los soldadores experimentados prefieren utilizar las siguientes marcas de máquinas de soldar: soldadura inversora Dispositivo Resanta (modelos 190, 200), Awelco (f5 - también con inversor), Vniissok (Mig-180), Fubag, Svarog, Kedr, Aurora.
Hay muchos vídeos en Internet que explican modelos de máquinas de soldar. Por lo tanto, si desea que la unidad esté equipada con ajustes automáticos de varios parámetros operativos y funcione correctamente, se recomienda que se familiarice con ellos.
Todos los entornos están interconectados. Para comprender correctamente las características de las relaciones, conviene estudiar la tabla.

Establecer la polaridad correcta
Configurar correctamente la polaridad en una máquina de soldar es lo más fácil. Los fabricantes siempre colocan carteles en las carcasas de las unidades que facilitan comprender qué polaridad (directa o inversa) es mejor elegir en una situación particular. Todo depende de los metales y aleaciones con los que interactuarás.
Para configurar la polaridad directa, conecte correctamente el quemador de gas al terminal con el signo “–”. Para configurar la máquina de soldar en modo de polaridad inversa, el soplete de gas se conecta al terminal con el signo “+”. Para simplificar, estos terminales se denominan “positivos” y “negativos”.
La polaridad se ajusta dependiendo del tipo de hilo que se utilice en la instalación en un momento concreto. Hay 2 opciones:
- El cable es sencillo. En este caso es sólido. Para utilizarlo para interactuar con diferentes metales, es necesario utilizar un gas protector. El hilo no tiene aditivos. La superficie de trabajo debe estar absolutamente limpia. Está permitido utilizar cables simples solo en interiores. Al usarlo, puede contar con la formación de una costura fina y uniforme.
- El alambre tiene fundente. La parte central del hilo tiene un aditivo especial. Está diseñado para formar un gas que realiza una función protectora. Por lo tanto, no es necesario utilizar adicionalmente otros gases protectores. Tampoco es necesario limpiar a fondo la superficie de trabajo. Puede interactuar con dicha soldadura al aire libre: un viento fuerte no le impedirá lograr una costura uniforme. Es cierto que, como resultado, se forma una gran cantidad de escoria, que deberá eliminarse.
Si utiliza una rosca normal de cobre, es correcto observar siempre la polaridad inversa y también conectarla al terminal positivo. Pero en este caso, se debe aplicar una carga negativa al metal que se va a soldar. Si el cable está equipado con fundente, debe tener polaridad directa. La conexión se realiza a través del terminal negativo. Sobre la pieza a soldar se coloca un terminal con carga positiva.
Configuración de la extensión del cable
Para configurar correctamente la máquina de soldar, también debes encargarte de ajustar la extensión del cable. El alcance se refiere a la distancia entre los extremos de la punta y el cable. Para simplificar, solo debes considerar la longitud que el hilo se extiende desde la punta.

Si logras configurar correctamente este parámetro del sistema, durante el funcionamiento podrás eliminar una gran cantidad de salpicaduras que hacen que la costura final sea desigual y estéticamente poco atractiva. La propia máquina de soldar también presentará menos vibraciones. La soldadura de estructuras metálicas se realizará correctamente: será posible evitar quemaduras y una resistencia insuficiente de la conexión de las láminas entre sí.
En el caso de utilizar diámetros pequeños, los parámetros de voladizo y salida son iguales entre sí. Si aumenta el grosor del hilo, entonces el parámetro de liberación debe reducirse entre 1 y 10 milímetros (según la situación).
Hay muchos tamaños de salida. Pero principalmente sólo se utilizan 3 opciones. Cada uno de ellos depende directamente del diseño que tenga una boquilla de gas en particular y del entorno protector que se utilice en la máquina de soldar actual.
Solo teniendo en cuenta estas características del proceso se puede configurar correctamente la máquina de soldar y establecer la longitud de extensión de cable requerida. Ahora directo a las opciones:
- En la mayoría de situaciones, la versión debe configurarse lo menos posible. Los valores medios son de 6 a 10 mm. El valor es adecuado en una situación en la que se utiliza dióxido de carbono (mezcla de argón) como medio protector durante la cocción del acero. A medida que aumenta la cantidad de argón utilizada, también aumenta la longitud de la salida.
- Si se decide utilizar argón puro como protección, el saliente del hilo de la máquina de soldar debe ajustarse correctamente para que sea superior a 10 mm. En algunos modelos el desbloqueo se ajusta automáticamente para obtener la mayor eficiencia en la soldadura de materiales.
- Si la punta de la boquilla está ubicada directamente en el cuerpo de la máquina de soldar (empotrada en ella), si configura el saliente demasiado corto, no se alcanzará el nivel requerido de fusión. Por eso es tan importante configurar este elemento correctamente.
Para comprender mejor cómo configurar correctamente una máquina de soldar, lo mejor es tener siempre esta tabla a mano.
Los fallos más comunes y sus síntomas.
Es importante configurar correctamente la máquina de soldar. De lo contrario, la calidad de la costura se verá muy afectada. O, peor aún, la propia máquina de soldar fallará. A continuación se presentan algunas recomendaciones de cerrajeros experimentados. Antes de configurar usted mismo la máquina de soldar, vale la pena estudiarlos.
- Si la tensión suministrada es insuficiente, la soldadura no penetrará lo suficientemente profundo.
- Si el material no se limpia lo suficientemente bien antes de soldar, la costura se formará entrecortada.
- No alejes demasiado el quemador. Si durante la soldadura se encuentra a una distancia de más de 12 mm del material, la costura se formará de forma intermitente.
- Si se aplica un alto voltaje, pero los materiales que se unen no son lo suficientemente gruesos, existe una alta probabilidad de que se quemen. Todo esto generará costos adicionales de tiempo y recursos destinados a eliminar el problema.
- Si no hay gas protector en la zona de soldadura, la costura se vuelve porosa y adquiere un tinte verdoso. Se sabe que la porosidad afecta negativamente la resistencia general de una estructura. Por eso no se debe permitir su educación.
- Debe trabajar con la máquina de soldar solo después de diagnosticar su estado. Siempre se debe realizar una inspección visual. Compruebe si existe alguna violación de la integridad de las partes vivas.
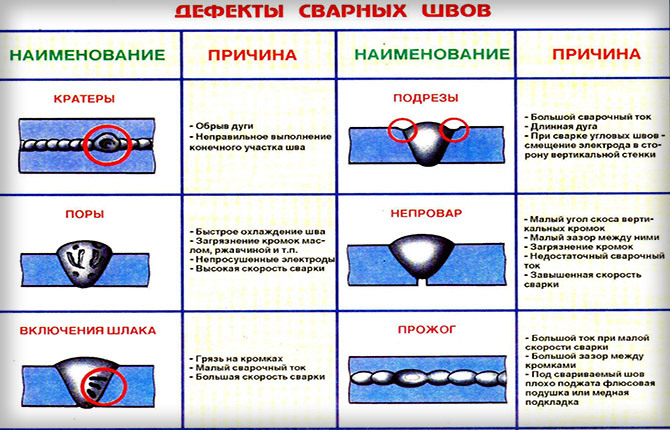
Es imposible trabajar sin máscaras protectoras de soldadura especiales que oscurezcan las llamas. Las máscaras de camaleón actúan como un filtro de luz para proteger contra destellos de alto brillo. Sin ellos no se puede trabajar: puedes dañar gravemente tus ojos.
Ahora no deberían surgir preguntas sobre cómo configurar correctamente la máquina de soldar. Debes seguir estrictamente las instrucciones y recomendaciones presentadas en el artículo. Sólo en este caso la unidad funcionará correctamente.
¿Cuánta atención prestas a la configuración de la instalación antes de trabajar? Asegúrate de compartir tu opinión en los comentarios. Guarde el artículo en sus favoritos. Quizás también te ayude a configurar tu dispositivo.