Do-it-yourself plasma cutter from an inverter is not a joke, and in fact, you can convert an old unnecessary inverter into a new fixture. On the one hand, it seems impossible to make a diametrically opposite device from an inverter. After all, the inverter is used to weld metal, and the plasma cutter is used to cut it. But lovers of converting existing devices have not disappeared on our land, so read a little lower in the article how to make a plasma cutter with your own hands.
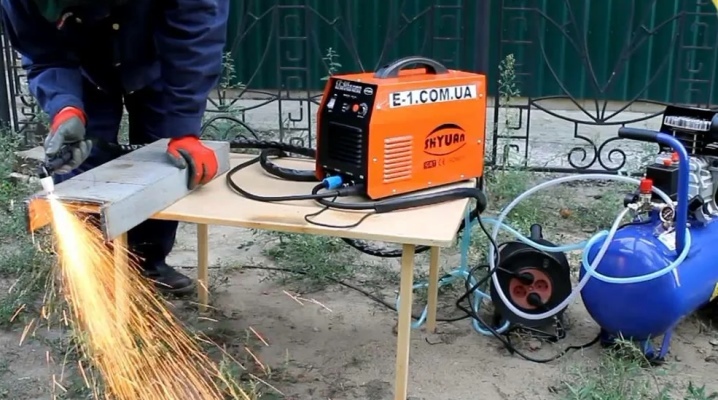
The content of the article
-
Do-it-yourself plasma cutter from an inverter
- How to assemble a plasma cutter with your own hands from an inverter
- Conclusion
Do-it-yourself plasma cutter from an inverter
In order to make a plasma cutter with your own hands, you will need:
- An old unnecessary inverter or some kind of transformer that acts as a source of electric current. Buy a new inverter impracticalbecause soAndIn the same way, you can buy a new plasma cutter.
- plasmaOthrone, aka special cutter for cutting methlla using plasma. Without a special cutter, a home-made plasma cutter cannot be obtained, because it is in it that a plasma arc is formed from electric current and air supplied under pressure. Individual amateurs make their own plasmaOa throne from an argon-arc welding torch, but it’s better not to experiment, but to purchase a factory copy, because this is a key and structurally complex part of the plasma cutter.
- A compressor that will supply air under pressure to the plasma stream to cool it. The compressor must be able to create a pressure of 4-4.5 atmospheres, so you can use any, even home-made. Almost any factory compressor is able to create a pressure of 6-8 atmospheres. The performance of the compressor will directly affect the thickness of the metal being processed. For example, for a thickness of 20 millimeters, the performance should be at least 170 liters per minute. In order for the plasma cutter to work more stably, the compressor receiver must be at least 50 liters.
- Hoses and electrical cable. Hoses and cables are needed to form the technical design of the plasma cutter. For example, you need an electrical cable to supply electricity to the plasmaOthrone and one more for the "mass". You also need a thin cable to form the pilot arc. Hoses are needed to supply air to the plasmaOthrone. In some cases, cables and hoses are used as separate elements, that is, a separate air hose and a separate electrical cable. But you can buy a ready-made factory cable-hose, where the electrical wires are placed inside the cablenha, through which air is supplied to the plasmaOthrone.
This is not to say that a plasma cutter is an indispensable thing at home. It makes sense to do a plasma cutter with your own hands when there is a large amount of work on cutting and cutting metal sheets. With small volumes of such work, a plasma cutter may not justify itself, because in the end it turns out to be an expensive product.
An inverter is most often chosen as a power source for a plasma cutter, rather than a conventional transformer. This is because the inverter is able to give plasma cutting a stable working process. The difference when working with a plasma cutter, where an inverter is used as a power source and a simple the transformer is the same as in welding work when an inverter is used as welding and normal welding. Welders love the inverter because of the stable and smooth working process. Plus, the inverter, with a small size and weight, is capable of delivering high power. By the way, there is a pattern in plasma cutters: the more powerful the power source, the more powerful the plasma flow, which means it will be possible to cut thicker metal.
How to assemble a plasma cutter with your own hands from an inverter

If you have the inverter itself, compressor, plasmaOthrone and bought a special cable-hose, then assemble everything as easy as shelling pears:
- Connect the air supply hose from the compressor to the inverter. Many inverters are equipped with this feature by default.
- Connect the cable-hose to the inverter. Connect the plasma to the other side of the cable-hoseOthrone.
- Connect the ground cable to the inverter.
After your own plasma cutter is assembled, you can start testing and working with it. The essence of using a plasma cutter is similar to the essence of using welding:
- you need to connect the ground cable to the metal that you want to cut with plasma;
- you need to turn on the compressor so that it pumps up the receiver and is ready to give out the necessary pressure;
- turn on the inverter;
- bring the plasmaOthrone to the metal and press the start button on it.
After such simple manipulations, you will be able to fully work with a plasma cutter made by yourself. At the moment of starting the button on the plasma torch, the following occurs:
- when the inverter is turned on, an electric current is supplied to the plasma torch;
- directly in the plasma torch itself, the current enters a special electrode, on which an electric arc is formed with a temperature of 6-8 thousand degrees;
- after that, air is supplied to the plasma torch nozzle under pressure, which passes strictly through an electric arc;
- the electric arc heats and “charges” the air flow that exits through the plasma nozzleOthrone.
Thus it turns out that from plasmasOThrone comes out plasma, which is essentially a "mixture" of air and an electric arc. The fact is that the temperature of this "mixture" at the outlet reaches 20-35 thousand degrees, which allows you to simply cut it when in contact with the metal.
Conclusion
Do-it-yourself plasma cutter from an inverter is a very real thing. The main principle when designing your own plasma cutter is to take care of your own safety. Therefore, it is better not to “do-it-yourself” completely, but to purchase a factory plasma torch with several spare nozzles that fail very quickly. You also need to purchase a factory cable-hose, which is also produced according to all standards. The fact is that the factory elements are able to withstand all the potential loads thate will occur during the operation of the plasma cutter, and "homemade" do not give such a guarantee.