Polyethylene pipes with a diameter of 2-120 cm are often used for laying water pipes, gas pipelines, and storm sewer equipment. They are durable, corrosion resistant, lightweight and easy to install. Welding is used to connect products. It can be of different types. The most popular is butt welding of polyethylene pipes. It provides a seam that is tight and aesthetically pleasing.
Usually, specialists are hired to lay the highway. But, you see, the services of a professional are not cheap? In addition, not all craftsmen are conscientious and responsibly approach the execution of the order. If you have certain knowledge and skills, then you can do the work yourself. This will save money and guarantee a quality result.
We will tell you about the technology of welding polyethylene pipes with the butt method, we will give a detailed algorithm actions, we will give links to regulatory documents and advice that should be followed when performing such work.
The content of the article:
-
How to do butt welding?
- Reflow welding
- Resistance welding
- What to choose for polyethylene pipes?
- Can I weld myself?
-
Butt Welding Instructions
- Preparation of welding equipment
- Creation of the necessary conditions
- Preparation of polyethylene pipes
- Butt welding
- Time to complete the process
- General advice on welding
- Conclusions and useful video on the topic
How to do butt welding?
Butt welding is popular today. This method is used not only in industry, but also in everyday life. It is used to join homogeneous workpieces. Butt welding has several advantages over other technologies.
For its implementation, couplings and other elements are not needed. This allows you to save a lot of money on the purchase of additional materials. The applied technology ensures the preservation of the indicators of flexibility and strength. With its help, you can connect pieces of products of different lengths. At the same time, the strength at the weld will not be lower than in other solid sections.
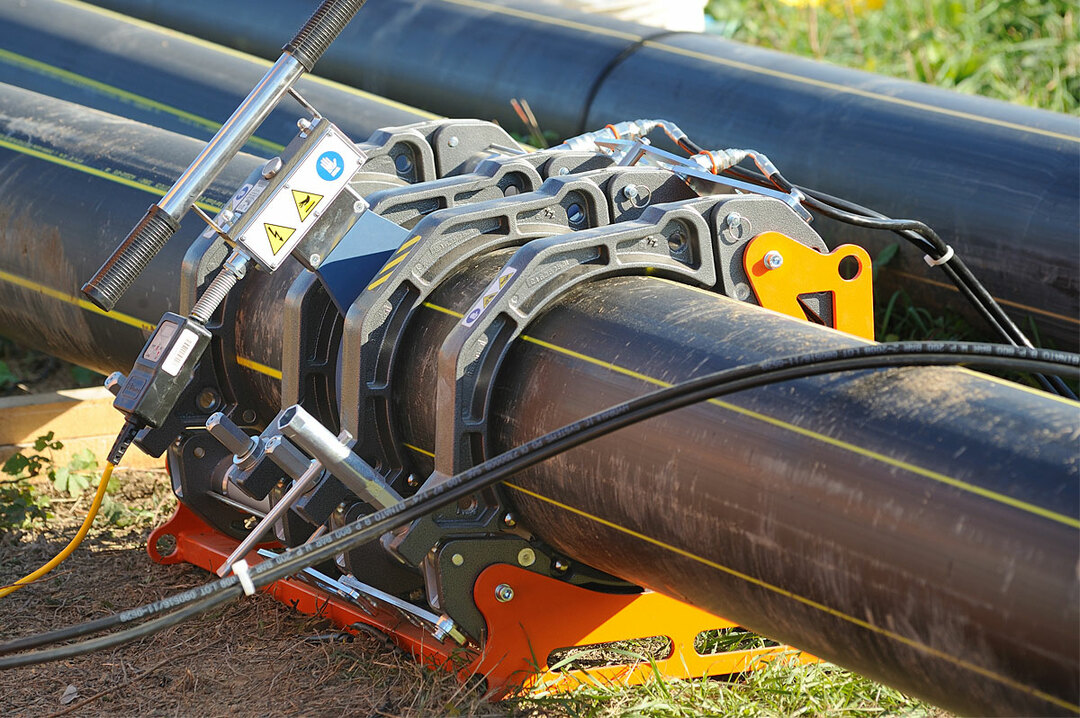
Butt welding of pipes refers to one-piece connection options. It can be performed using different technologies. The optimal method is selected based on the material of manufacture of the line
Butt welding can be performed by means of reflow and resistance. Each of the options has its own characteristics, pros and cons.
Reflow welding
The essence of welding with this method lies in the fact that the pipe joints are melted under the influence of a heated tool until they become viscous. Then the ends are connected under pressure and kept until they cool completely. The result is a tight seam.
In order for the connection to be of good quality, it is necessary to tightly press the pieces of the product after heating. The use of modern equipment makes it possible to partially automate and simplify this work. With its help, the operation of connecting pipes by the method of flashing is carried out in the shortest possible time.
Resistance welding
The essence of resistance butt welding is that the edges of the pipes are pressed against the electrodes, which are equipped with special jaws. This provides a high quality electrical contact. Material slippage between the electrodes is excluded.
Then the two pipes are pressed tightly against each other and fixed. Next, the welding current is supplied. The contacting areas of the material are melted and combined under pressure into one product. The resulting design has low oxidation resistance during operation. This significantly limits its scope.
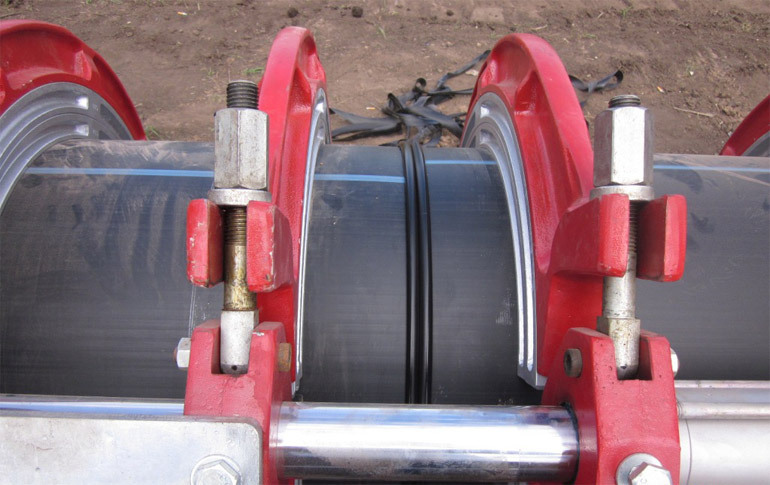
Resistance welding is commonly used to join thin mild steel parts (pipes, rods, wires). It is also used to weld copper, bronze and brass elements.
Resistance welding is only suitable for pipes with small cross-sections. Therefore, in large-scale production, for laying large highways, it is rarely used.
What to choose for polyethylene pipes?
Often polyethylene material is used for laying the pipeline. This is due to its low price and excellent performance characteristics.
It is worth remembering that polyethylene is a dielectric. Therefore, unlike metal, it does not conduct current. To connect products from it, it is recommended to use the reflow method. Using the method of butt welding with resistance on polyethylene, it will not work to make a seam. It is necessary to use equipment that heats the sections of the two parts.
Reflow welding of polyethylene pipes has a number of features. First, the parts are brought together at a low speed. Secondly, the tension remains unchanged throughout the entire process. Thirdly, all microroughnesses disappear due to the uniform supply of the elements to be joined. Fourthly, to ensure the maximum contact area, the surface of the workpiece is melted.
Can I weld myself?
Laying a polyethylene line by butt welding has its own characteristics and differences from other methods of joining two products.
To carry it out, you need certain knowledge and experience. Otherwise, the design will come out of low quality and short-lived.

Do-it-yourself butt welding can be done. But for this you need to know the essence and features of this process. Welding skills are important. Otherwise, you can only ruin the plastic pipes and waste time.
The butt welding method is not easy to implement. Not everyone is able to connect pipes efficiently the first time. If there is no knowledge and skills in the field of welding, then it is better to contact a professional master for laying the line. But for the work he will have to pay an impressive amount.
If a person has previously carried out welding by other methods, for example, electrofusion, then he will most likely be able to master butt technology. So it makes sense to try to hold connection of polyethylene pipes on one's own. But it should be borne in mind that the technology of butt welding is more complicated than in the case of connecting polyethylene pipes with an electric coupling.
To do the work efficiently with your own hands, you need to have special equipment. It can be rented. It will be much cheaper than buying a new or used machine. It is important to know and follow the step-by-step instructions for butt-weld reflow.
Butt Welding Instructions
Butt welding using reflow technology is used to join polyethylene products, in particular pipes. It is also used for installation fittings and other details.
For hard-to-reach, difficult areas, this method is not used. In such cases, electrofusion welding is more suitable.
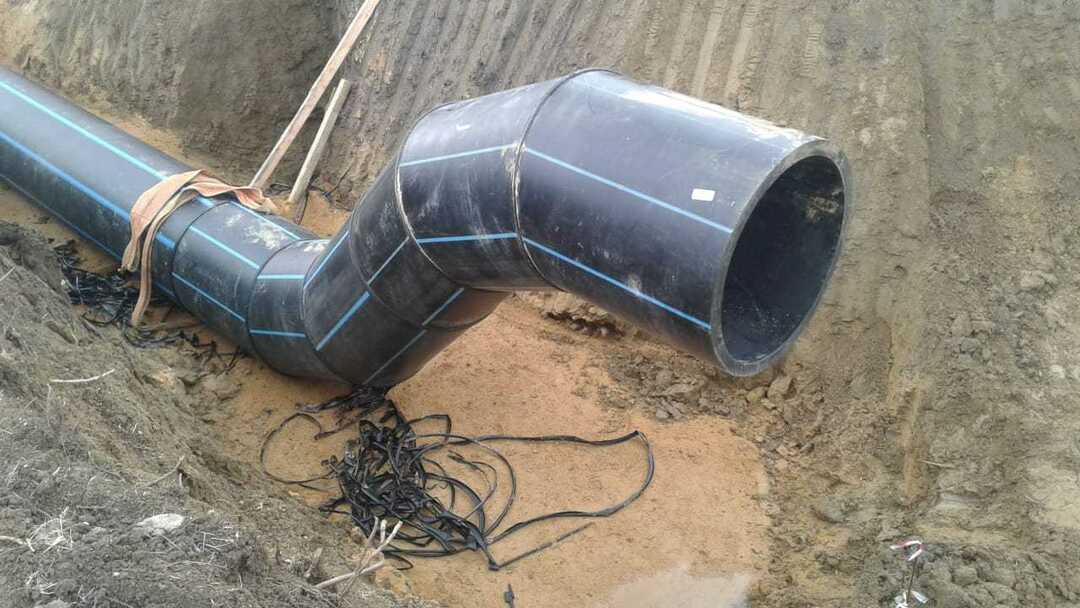
Thanks to butt welding, you can quickly create a water main. In this case, the design will turn out to be neat in appearance and durable. You can not be afraid of a leak at the junction
In order for the butt welding to be successful and the seam to be neat and durable, it is necessary to adhere to a certain algorithm of actions.
The step-by-step instructions are given below:
- Prepare welding equipment.
- Arrange the necessary conditions.
- Prepare pipes.
- Carry out welding work.
- Wait for the material to cool down and fix the result.
Each of these stages has its own characteristics, rules of conduct. We will discuss them in more detail below.
Preparation of welding equipment
To weld two pieces of polyethylene pipes by joining, special equipment is required. It centers, bends, melts and joins the edges of the products under the right pressure.
The modern market offers a wide selection of such devices. There are devices with mechanical, hydraulic drive and those that are equipped with software control. The latter are more convenient to use.
Butt fusion machines are of a standard design. They necessarily include the following components: centralizer, trimmer, heating element, reduction liners, drive.
The centralizer is designed for fixing the workpieces in the desired position and securing the ends of the polyethylene pipes to be connected. It is equipped with two movable and two fixed clamps.
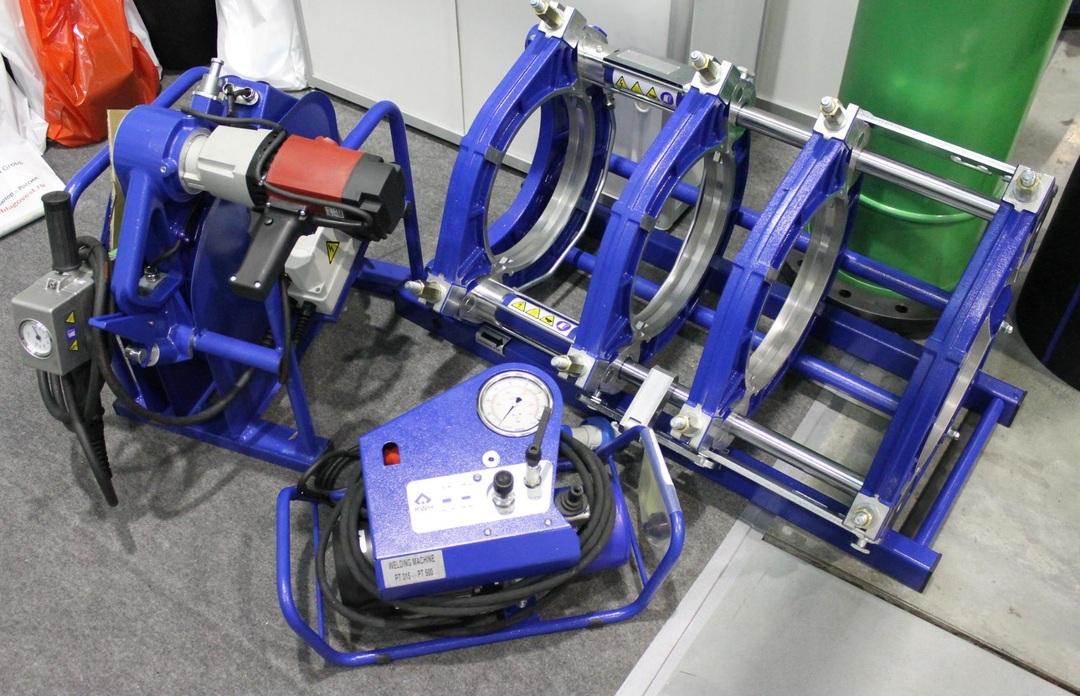
Butt welding equipment is used to join pipes made of PE100, 100+, PE 63 and PE 80 polyethylene. Such devices have been used for over 50 years.
The facing tool allows you to cut the cut so that the ends of the two parts are in full contact. According to the rules, a gap of no more than 0.05 cm is allowed for pipes of medium and small diameter.
For large items, this value increases to 0.07 cm. If, after the first processing during joining, the gap is greater than the established standard, then the facing tool is again used.
The heating element is in the form of a Teflon coated plate. It follows the shape of the pipe. The drive brings together and connects the heated and melted joints of two products. Gear inserts prevent product deformation.
Automated equipment has a control unit equipped with buttons. Such devices provide simplicity and accuracy of the welding process. This eliminates the possibility of making a mistake.
It is enough just to correctly position the two pipes that need to be connected and press the corresponding button. Modern equipment is highly efficient, but expensive.
Creation of the necessary conditions
The technology of butt welding by the method of flashing is simple to use. But it cannot be applied in all cases. It is important to fulfill a number of conditions.
Butt welding is possible only for pipes that are made of the same type of polyethylene and which have the same diameter. The wall thickness of the product should not be less than 0.5 cm. It is permissible to perform work only at a certain temperature range: from -15 to +45 degrees.
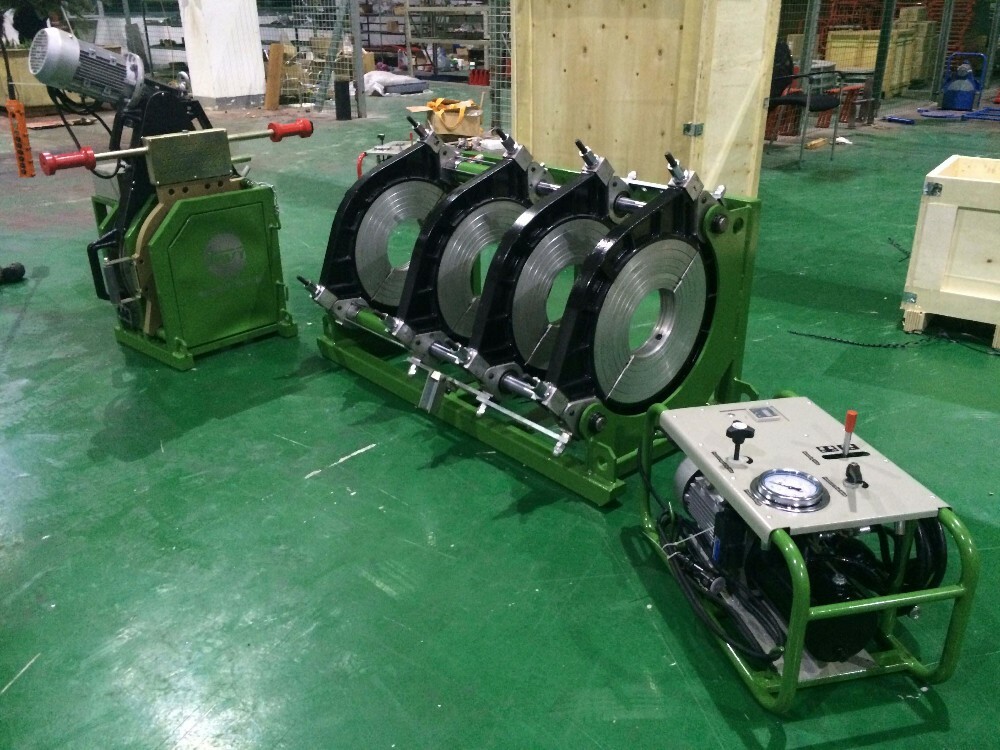
Temperature conditions are very important for butt welding. The result of the work depends on it. Easier to achieve optimal conditions for indoor welding
The butt welding method is implemented only if it is possible to reliably fix and press the ends of the pipes to be joined together. If you have a special apparatus, this does not arise with this problem.
Preparation of polyethylene pipes
To obtain a high-quality, airtight and aesthetic seam when connecting polyethylene pipes with a butt-welded method, you must first prepare the products. The ovality of the polyethylene pipelines should be checked. It is recommended to compare the wall thicknesses. It should be the same.
Also, the products should be prepared mechanically. For this, trimming, milling is used. This will allow the pipes to be connected in the desired position.
It is recommended to use an electric miter. He will cut the pipe at the desired angle. It is important that the edges of the workpieces are even and completely in contact with each other.
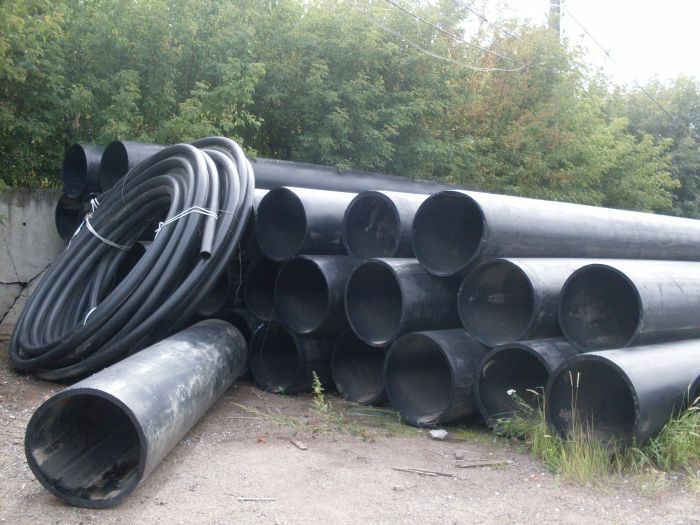
Do not skip the cleaning phase of the pipes, even if they are new. Dust accumulates on the product during transportation and storage. The presence of dirt particles will make the weld seam sloppy and leaky.
It is necessary to remove dirt from the surface of the parts - dust, dirt, etc., moisture. This may require two soft, dry rags and a special cleaning agent.
Butt welding
Butt welding by flashing and then connecting two parts on their own is best done in automatic mode. This will ensure the desired result is obtained.

If mechanical welding equipment is used, it is best to work with a partner. This will allow you to meet all the time standards at each stage of the process, to achieve a high-quality and reliable seam.
Regardless of whether automatic or mechanical equipment is used for butt welding, the procedure will be the same.
The process is performed in the following order:
- place the two pipes to be welded together in the centralizer and fix them. There should be a distance of about four centimeters between the products;
- to remove the chamfer and clean the products;
- Heat pipe ends at the same time with a welding mirror. The polyethylene material is usually melted 2 mm. This happens quickly enough;
- carefully remove the heating element;
- tightly connect the heated joints of the pipelines and fix them in this position;
- withstand under pressure.
As a result, you should get an even tight connection with external fusion in the seam area.
Time to complete the process
Flash welding of polyethylene pipes followed by joining can take a different amount of time. Much depends on the outer diameter of the workpieces. The larger it is, the longer the material heats up and cools, the more time is given to join.
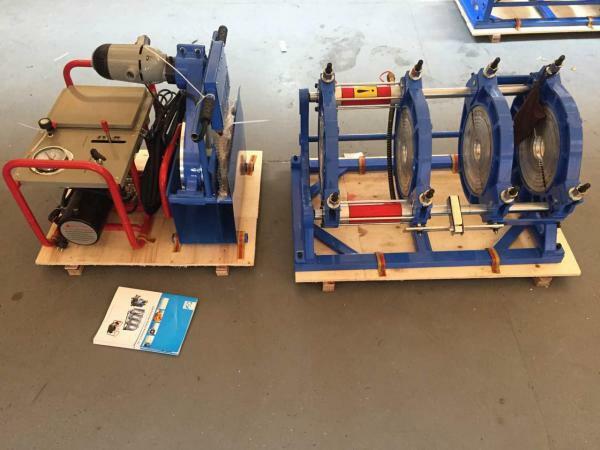
Before starting butt welding, you must carefully read the operating instructions for the equipment. Otherwise, questions may arise when using the device. Each stage of butt welding (heating, joining, holding under pressure) must be carried out in accordance with the established time standards. If, for example, you do not join the heated pipe ends for too long or remove the retainer too early, then all the work will go down the drain.
To obtain a strong, tight and neat seam, it is important to know how much you need to heat the ends of the pipes, to withstand the joined products. Similar information is shown in the table below.
Pipeline diameter in centimeters | Time for heating the ends of the workpieces in seconds | Time allotted for connection in seconds | Time to cool the joined pipes and obtain a reliable seam in minutes |
11,0 | 50 | 12 | 8 |
9,0 | 40 | 11 | 8 |
7,5 | 30 | 10 | 8 |
6,3 | 24 | 8 | 6 |
5,0 | 18 | 6 | 4 |
4,0 | 12 | 6 | 4 |
3,2 | 8 | 6 | 4 |
2,5 | 7 | 4 | 2 |
2,0 | 7 | 4 | 2 |
1,6 | 5 | 4 | 2 |
Most often, butt welding is used for polyethylene pipes with a diameter of more than 5 cm.
General advice on welding
When welding polyethylene pipes by reflow, it is very important to follow the instructions. Departure from technology can lead to overheating of the material and the appearance of an internal influx. This will disrupt the movement of fluids through the pipes.
Also, the seam may turn out to be crooked, inhomogeneous. In any case, such a design will be considered defective and unsuitable for use.
There are a number of recommendations that you need to adhere to in order to achieve the desired result. It is important that the walls during joining do not move by more than 10% of their thickness. When the material cools down, the connected parts must be securely fixed. The time taken to remove the heating plate and join the two ends of the product should be kept to a minimum.
Butt welding of gravity sewer pipes made of polymer by the butt method is not recommended. A bead forms at the junction, on which solid particles can accumulate, leading to blockage of the line.
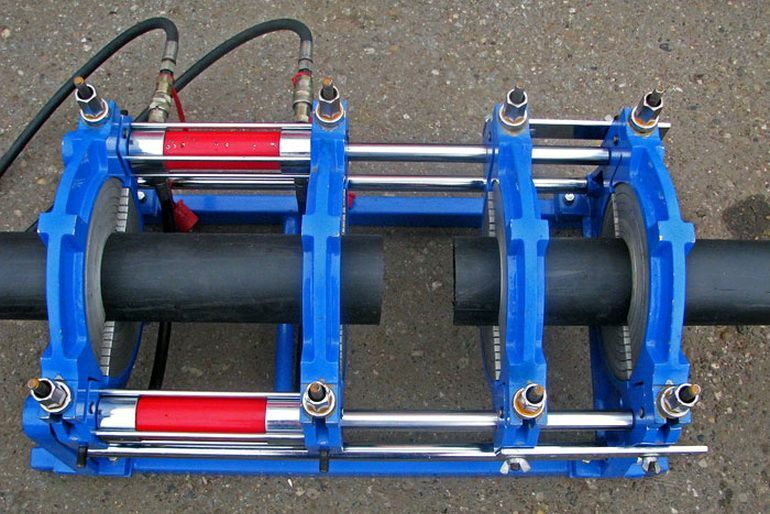
Butt welding of polyethylene pipes is not an easy task. Only by following the instructions and adhering to the recommendations of experienced craftsmen, it will be possible without unnecessary problems and as quickly as possible to create the necessary reliable structure
Having decided to lay a pipeline and carry out butt welding, it is recommended that you first familiarize yourself with the provisions of the relevant GOSTs. These documents contain rules, requirements for the quality of work, product.
When installing water and gas mains, you should focus on GOST R 55276. It describes the technology of butt welding of a polyethylene pipeline.
In relation to equipment for joining products by a similar method, the following applies. GOST R ISO 12176-1.
Conclusions and useful video on the topic
Procedure and features of butt welding of polyethylene pipes using a mechanical apparatus:
Butt welding of polyethylene pipes using automatic equipment:
In practice, butt welding of polyethylene pipes with your own hands is not very common. This is due to the fact that to perform such work requires special equipment, a certain level of knowledge and skills.
Butt welding of polyethylene pipes should be carried out in accordance with the established requirements and rules. This will ensure a high-quality and durable design. Butt welding has its own technology, features and differences.
You can implement the method yourself, but for this it is important to create the necessary conditions, properly prepare the pipes. If there is no welding machine, then it is more expedient to rent it. It is recommended that you familiarize yourself with the video on the subject of butt welding in advance. It will be easier to understand the essence of the method and the peculiarities of its implementation.
Do you have experience in butt welding of polyethylene pipes? Do you want to share your knowledge in this area or ask questions about welding? Please leave comments, take part in discussions - below is a feedback form.